OUR PROCESS
1. CONTACT
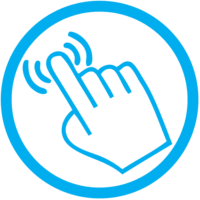
To start your custom skis, contact us via phone, email, or complete a Custom Fit Form on our website. A design expert will address your inquiry within 1-2 days.
2. CONSULTATION
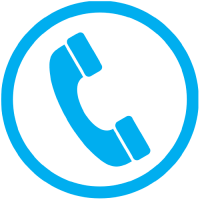
We will set up a convenient time for an in-person or phone consultation and work one-on-one with you to design your ideal skis.
3. BUILD
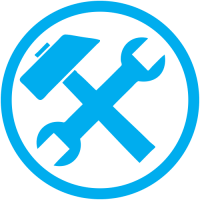
Relax while we construct your new custom skis. Current turnaround time for new custom orders is 3-5 weeks from when all build information is secured, including graphic choice.
4. RIDE
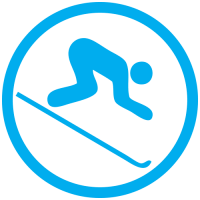
Enjoy your skis with the peace of mind knowing you’re covered under our 2-year 100% satisfaction guarantee.
Note: If you already know exactly what you want, feel free to complete your purchase in our online store.
DESIGN & CONSTRUCTION
SHAPE

The shape refers to the geometry and tip-waist-tail dimensions of the ski. Whether you’re looking for a narrow carving ski, a floaty powder ski, or anything in between, chances are we have a shape that’ll perform great for your skiing. If none of our geometries fit your bill, ask us about developing a fully custom shape, completely unique to you.
CAMBER / ROCKER PROFILE

Camber is the height of a ski’s center with respect to the ground, while rocker is the height of the tip and tail. Camber lends itself to a snappier, more carving-friendly ski, while rocker allows for more ease between turns and a floatier ski for soft, deep snow. Click here to view our standard camber profile offerings.
TAIL SHAPE

Tail shape depends mostly on a skier’s style and has less effect on a ski’s performance. A freeride oriented skier would typically prefer a round tail, while a frontside / carving oriented skier would prefer a flat tail. And of course a swallowtail is best for a surf-inspired, deep snow ride.
CORE BLEND

The wood types that make up your core are the primary structural components of your skis and dictate their personality. Optimally balancing weight, stiffness, and dampness.
Poplar & Bamboo – light and lively, our go-to for playful, all-mountain skis
Maple, Poplar, & Bamboo – added stiffness and damping for narrower geometries and heavier, more aggressive skiers
Aspen & Bamboo – out lightest core blend for weight-conscious skiers and uphill / touring setups
FLEX INDEX

A simple bi-product of your height and weight that translates physically to the thickness of your core. ~80% of customers fall into our “Standard” categorization.
Soft – our thinnest core profile, most forgiving
Standard – suitable and supportive for most customers
Stiff – Our thickest core profile for an aggressive flexing ski
COMPOSITE

The composites that laminate your ski materials together, again balancing weight and dampness. Our scale defines composite as the ratio of fiberglass to carbon fiber.
90 / 10 Glass Carbon – our standard resort blend and dampest offering
70 / 30 Glass Carbon – a slightly lighter option with 20% more carbon for the weight-conscious skier
100% Carbon – full carbon laminate for lightweight, dedicated touring skis
TESTIMONIALS
We asked a handful of clients for honest, in depth feedback. Here’s what they had to say.
Orhun Kantarci – 172 cm Cash 106
DESCRIBE THE FOLSOM CUSTOM FIT PROCESS:
Amazing. Mike and I had a long email contact and face to face session. The latter included my wife. One has to do their homework and know what they want their ski for so he can direct you. We did that. Of course he can also start from scratch with you. He is a non-assuming person. If you feel intimidated that Custom is only for pros you would be wrong. With Folsom it seems like it is all about having fun and sharing the fun with similar minded people. There is how should I say a, feasibility about the process and it is very comforting. He ultimately suggested working from the new for 2018 Custom Cash 106 mold. We met up got the demos. We got our new boots (specifically fitted for our needs for 50:50 Randonee + inbounds set-up). Once we got the feel for the changes we went through them and next time we met up picked up the skis, they were like custom made for our movement (well they were). First minute on the slope they felt like and extension of our legs. The custom graphics is anothe bonus. This sounds expensive but it really isn’t. Think about demo skis for 5 days for two people. Imagine you had two skis you narrowed down to and did that for 10 or so days to get a feel. Choose form any available 50:50 packages from the commercially viable big names. The cost of all that you need to subtract from the ultimate package you get from Folsom and you end up about the same price for something that is truely customized to you vs. closest fit.
DESCRIBE YOUR SKIS’ PERFORMANCE:
I understand that everybody’s needs are different. We are advanced skiers but our days of any sort of jumping or killing it down an icy run etc is behind do to injuries. However we now enjoy responsive controlled carving in any condition. We are not in a rush. The skis were just that from ice to not deep powder (the real powder testing will wait for next year but I am not worried about it a bit ). Bindings we put on were tectons. Boots we use are Solomon mtn lab for me and scarpa gea RS new one for my wife. Larry as in bootfitter Larry sold and fitted them for us. Everything as is works together perfectly.
Dan Joseph – 188 cm Primary
DESCRIBE THE FOLSOM CUSTOM FIT PROCESS:
I’ve been skiing for over 30 years. As a telemark skier for 20 of those years. I was looking to “dial in” all of the good things from skis past and current to hopefully come up with the ski that fit me like a glove. From deciding which ski shape and profile to tweaking the amount of camber and sidecut to get it just right – Max and the team at Folsom were absolutely the best. When it came time to choose the graphics – he even helped me with adding that little special touch to make them my own. The entire process could not have gone any better!
DESCRIBE YOUR SKIS’ PERFORMANCE:
The skis are just plain awesome. I wanted a ski that was capable of making short quick turns but was also capable of ripping longer GS type turns while being stable at speed and I got just what I wanted. The subtle rocker but with camber is the perfect combination of fun. Sometimes when I want the skis to feel solid and hooked up like I’m on rails – they’re there when I need them. Finish it all off with a width that handles the fluff with style – I couldn’t be more pleased. Can you tell I like them??
Eliza Kubok – 177 cm Gambit
DESCRIBE THE FOLSOM CUSTOM FIT PROCESS:
It was exceptionally helpful to make the ski fit my skiing style. My husband knew I needed bigger skis, but I was still about to get a light and flexible design that makes skiing so easy.
DESCRIBE YOUR SKIS’ PERFORMANCE:
They perform best in powder, however they are definitely an all mountain ski. They’re so light and the skis quickly react to my guidance. I absolutely love them. Not being such a tall person, having custom skis are the answer, as I can have big and tall skis but due to their light weight it’s still easy to enjoy deep powder turns. The ski has my also cat on them which is a positive addition to being able to enjoy my animal’s calming looks while I ski some I tense terrain!
Have a testimonial? Share it with us here and receive a free gift!