Building skis is a very messy process that produces a lot of waste. Every ski manufacturer out there, big and small will all admit that building skis is not an environmentally friendly activity. The vast majority of skis that are built using modern day technology and techniques use epoxy, fiberglass, carbon fiber, and multiple grades of plastic at a bare minimum. There are a handful of very small manufacturers that have been able to change the raw materials needed to make skis into eco-friendly substitutes; however they are certainly a minority.
Quality aside, building skis produces lots of waste that is very difficult to recycle. In this blog, we’d like to show you the ways that we here at Folsom Custom Skis reduce our carbon footprint. This is mainly done by buying FSC certified woods for our cores, use excess core material for other products rather than throwing them away, and recycling any paper and plastic materials that we wouldn’t use otherwise. So let’s get into it!
Ski Core Woods
The primary woods that we use for our ski cores are Poplar, Maple, Bamboo and Aspen. While we vertically laminate the cores in house at our Denver Headquarters, we get the wood from a local supplier in the Denver area, Austin’s Hardwoods. All of the wood that we purchase is FSC (Forest Stewardship Council) certified which means that it’s not only the highest quality wood that we could be using, but also that the wood is sourced in an environmentally friendly manner. The Forest Stewardship Council is a nonprofit organization that is dedicated to promoting responsible forestry. Any wood with an FSC certification stands for high quality, and that the forest that it was harvested from is responsibly and appropriately managed as to decrease it’s environmental impact.

We also only get our wood from a local Denver producer, and all of the wood is harvested right here in North America. Our Poplar comes from the Eastern US, our Maple comes from the Northeast of North America, and our Aspen is sourced either From Canada or the Northern US; all of which is FSC certified, sent to our Denver producer where it’s cut to appropriate lengths for us to make our cores out of.
With so many shape and length options for customers to choose from, each and every core that get’s made in-house is a different size, which can leave excess material. Rather than simply disposing of the excess wood, we take the larger excess pieces to make coasters. They’re made from the exact core combinations that are available to our skis, and helps to reduce our waste that may otherwise be turned into fuel, thus emitting more carbon dioxide, nitrous oxides, sulfur oxides, etc. While the larger pieces are turned into coasters in-house, our skinnier excess pieces are currently being recycled at a local Denver plant that ensures it gets turned into a soil conditioner so its nutrients are spent wisely.
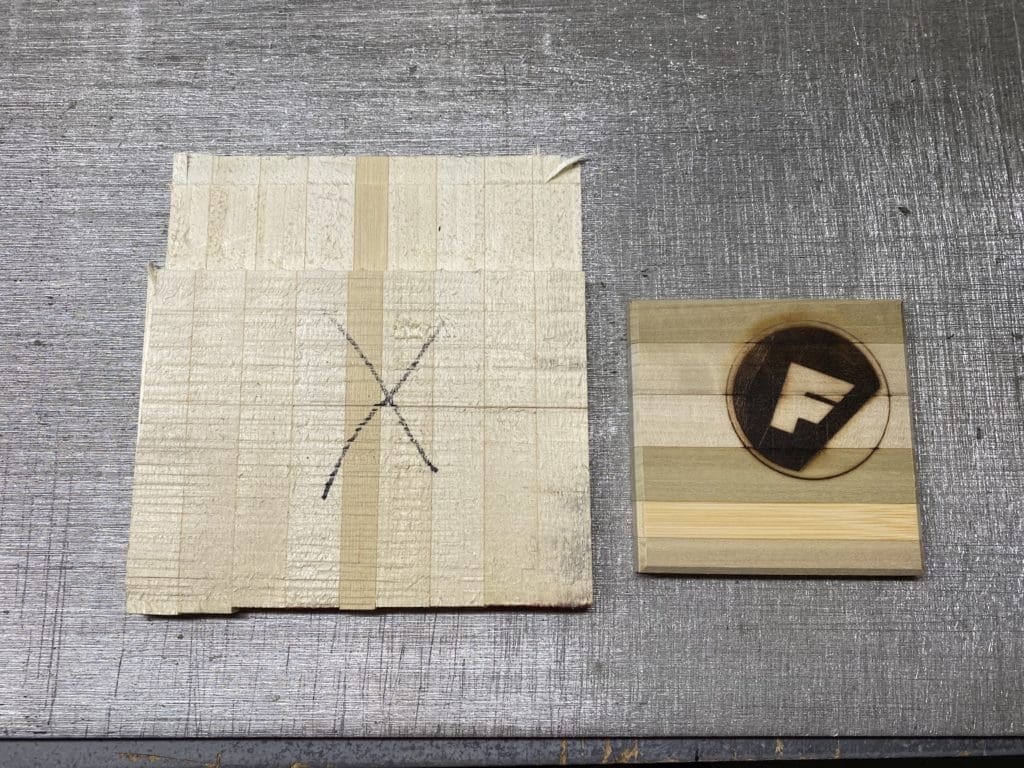
PPE Cashier’s Shields
Recently, we have added many PPE (Person Protective Equipment) products to our shop due to the high demand for them in the medical field, and for retail locations and restaurants that have been reopening. Most of these products are either created from plastic like our PPE Face Shields, or polycarbonate and acrylic like our PPE Cashier’s Shields. Thankfully with the Face Shields, we were able to utilize 98% of the plastic and materials we acquired for production; so that waste is a minimum. Any of the excess plastic was taken to a Denver recycling plant where the polyethylene that makes up the shields can be reused.
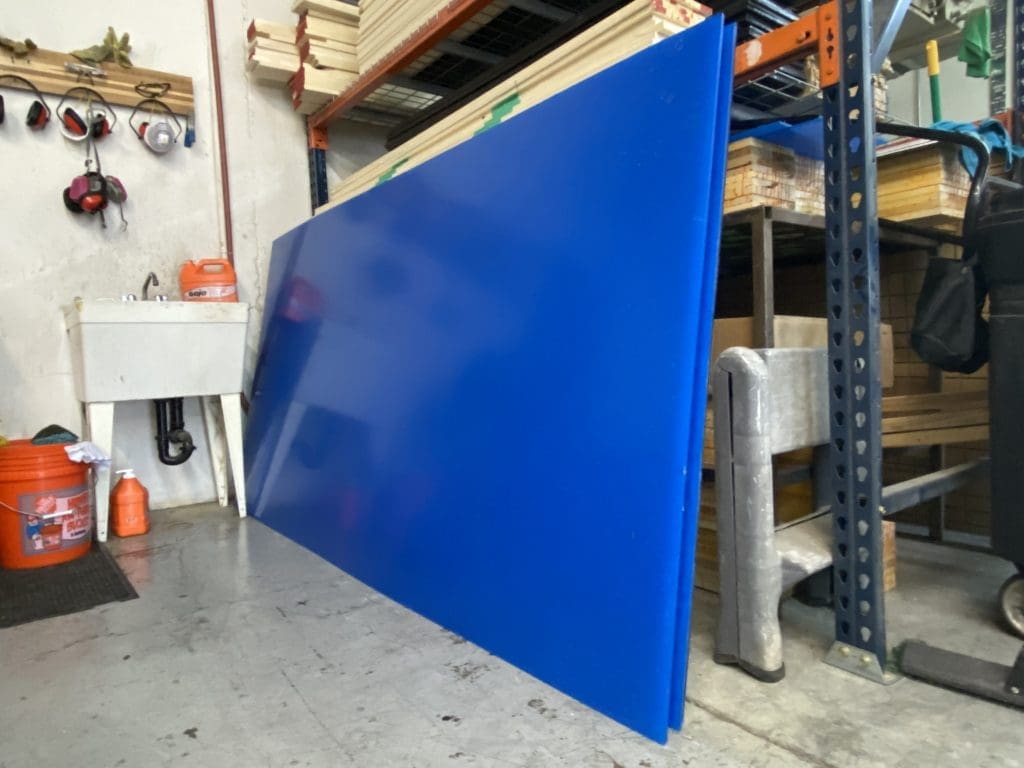
Our Cashier’s Shields are a little more complex, especially with custom orders being available, and unfortunately produce more waste. However, the materials we use to produce these shields, polycarbonate and acrylic, are fully recyclable and acrylic is infinitely recyclable. So once we have used a sheet of material to cut the shields we need, we take all of the excess material right back to our friends at Polymer Shapes, where they can recycle and reuse the acrylic and polycarbonate for future use.
Topsheets
All of the topsheets we make at our Denver manufacturing headquarters are made through dye sublimation. Essentially, this process involves printing the ski design on dye sublimation paper with dye sublimation ink, and then using heat and pressure to get the design to transfer (sublimate) into the topsheet material. Once the design is transferred, we are left with a useable topsheet and an excess piece of paper. Rather than throwing away the paper, we recycle it by using it as packaging material for any of our skis or PPE products that are shipped out. While it is beneficial to recycle that paper, we have decided to use this paper for packaging material rather than order new packaging specific paper to help balance the amount of materials coming in and going out of our Denver Headquarters.
We do ask that customers who receive their skis recycle that paper as it’s very environmentally friendly to do so. Recycling paper that can then be used to make more paper involves anywhere from 28% to 70% less energy use than using virgin paper. In the grand scheme of things, this adds up to a lot of energy being saved and compounds over time to a net benefit for everyone, as there’s less pollutants being emitted into the air.
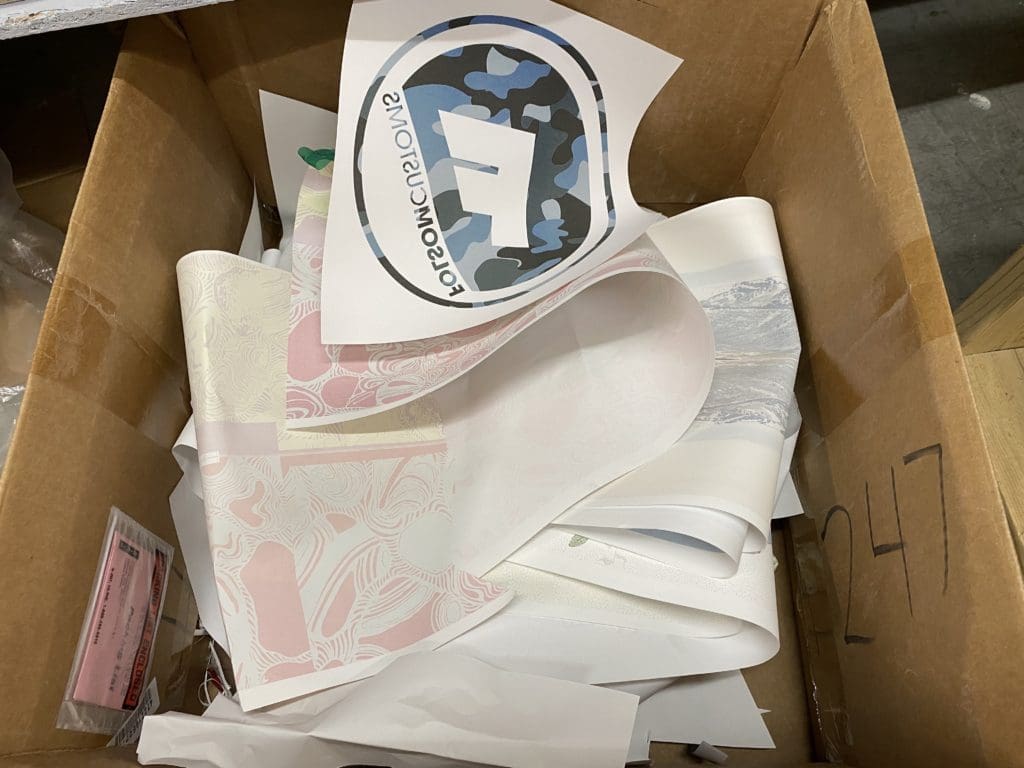
We’re not Perfect
At the end of the day, we have to recognize that ski building is a messy business. Above is a list of the major recycling techniques we use, but not 100% of every raw good that comes into our shop can be reused or recycled. All of that being said, for a ski manufacturer our carbon footprint is very small. As a small team of 5 guys, two of which come from Environmental degrees and backgrounds, a 4000 square foot operating space and plenty of access to local recyclers, we are doing our part to make sure that there will be skiing in the future. If you have ways to recycle raw goods such as fiberglass, epoxy, base material, etc. feel free to contact us and help us reduce our waste even further.
With locally sourced woods, 100% of our production being handled in-house, and a small team of dedicated skiers and environmental stewards, you can trust that your skis are going to be the highest quality possible and that the footprint of Folsom Skis is much smaller than the retail skis you’ll find at any ski shop. Check out our shape offerings and fill out a Custom Fit Form today so that you can get the perfect pair of skis for you, and help reduce the impact that the ski industry has on the climate.